385Mm Length TCT Material Plastic Cutting Blade For Grinding
Machine
Description:
The key performance advantages of granulator blades are:
1,High Hardness and Wear Resistance:
- Granulator blades are subjected to significant abrasive wear during
the size reduction process, especially when processing hard,
fibrous, or abrasive materials.
- Blade materials like alloy steel, tungsten carbide, and ceramic
possess exceptional hardness, which helps maintain a sharp cutting
edge and extend the blade's service life.
2,Impact Toughness:
- Granulators often operate under high-impact conditions, with the
blades encountering sudden loads and stresses as they interact with
the feed material.
- Blade materials with high impact toughness, such as alloy steel,
can withstand these dynamic loads without chipping, cracking, or
breaking, ensuring consistent performance and reliability.
3,Thermal Stability:
- The granulation process can generate significant heat, which can
affect the structural integrity and cutting performance of the
blades.
- Blade materials with good thermal stability, like alloy steel and
high-speed steel, can maintain their hardness and strength even at
elevated operating temperatures, ensuring consistent and efficient
size reduction.
4,Corrosion and Chemical Resistance:
- In certain applications, such as pharmaceutical, food, and chemical
processing, the granulator blades may be exposed to corrosive or
chemically aggressive environments.
- The use of corrosion-resistant materials, coatings, or specialized
surface treatments can protect the blades and prolong their service
life in these demanding environments.
5,Consistent Particle Size Reduction:
- The blade design and material selection can significantly impact
the consistency and uniformity of the granulated product.
- Carefully engineered blade profiles, combined with high-performance
materials, can achieve precise and consistent particle size
reduction, meeting the specific requirements of the application.
6,Energy Efficiency:
- The selection of high-performance blade materials can contribute to
improved energy efficiency in the granulation process.
- Durable and wear-resistant blades require less power to maintain
their cutting performance, resulting in lower energy consumption
and operating costs.
7,Reduced Maintenance and Downtime:
- Granulator blades made from materials with superior wear resistance
and impact toughness require less frequent replacement and
maintenance.
- This can lead to reduced operational downtime, lower maintenance
costs, and improved overall equipment effectiveness (OEE) in the
granulation process.
Granulator Blade Specifications:
Product Name: | Granulator Blades Manufacturer For Recycling Crusher Machine |
Material | SKH-51 |
Length | 100mm |
Width | 10mm |
Thickness | 3mm |
Hardness | HRC 54-62 |
Precision | ±0.02-0.04mm |
Application | All kind of plastic |
When selecting granulator blade materials for specific
applications, the key factors to consider include:
1,Material Hardness and Wear Resistance:
- The abrasiveness and characteristics of the feed material (e.g.,
plastics, pharmaceuticals, minerals) determine the required
hardness and wear resistance of the blade material.
- Harder materials, such as alloy steel, tungsten carbide, and
ceramic, are often selected for applications with highly abrasive
or dense feed stocks.
2,Impact Toughness:
- The granulation process can involve high-impact loading on the
blades, especially in applications with large, dense, or
irregularly shaped feed material.
- Materials with high impact toughness, such as alloy steel, are
preferred to prevent chipping, cracking, or breaking of the blades.
3,Thermal Stability:
- The heat generated during the granulation process can affect the
blade's hardness, strength, and dimensional stability.
- Materials with good thermal stability, like high-speed steel and
specialized alloys, are chosen to maintain consistent cutting
performance at elevated temperatures.
4,Corrosion and Chemical Resistance:
- In industries like pharmaceuticals, food processing, and specialty
chemicals, the blades may be exposed to corrosive or chemically
aggressive environments.
- Corrosion-resistant materials, such as stainless steel or
titanium-based alloys, are often selected to ensure compatibility
and extend the blade's service life.
5,FDA/Food-Grade Compliance:
- For applications involving food, pharmaceutical, or nutraceutical
products, the blade materials must be approved for direct or
indirect food contact and meet relevant regulatory requirements.
- Stainless steel, ceramic, and specialized food-grade coatings are
commonly used in these applications.
6,Cost-Effectiveness:
- The initial cost of the blade material, as well as the long-term
operating and maintenance costs, are important factors in the
selection process.
- The balance between performance, durability, and cost-effectiveness
is crucial, especially in high-volume or cost-sensitive
applications.
7,Manufacturability and Machinability:
- The ease of fabricating and machining the blade material can impact
the overall production costs and lead times.
- Materials with good machinability, such as certain alloy steels,
may be preferred to simplify the manufacturing process and reduce
costs.
Picture:

Size:

Applications:

Packing & Delivery:
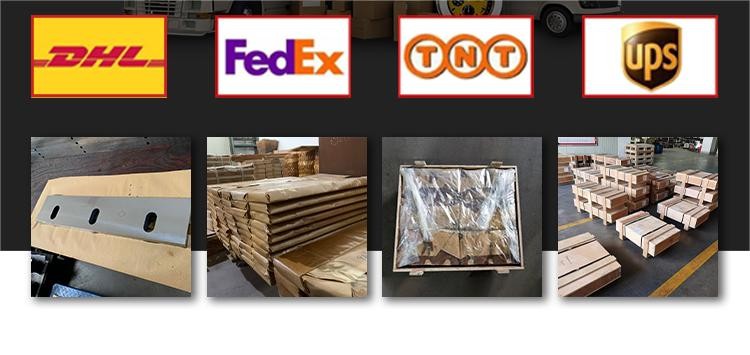