568 X 100 X 22mm Alloy Tool Steel D2 Granulator Screens Plastic
Shredder Parts
Description:
Here are the key basic information points about granulator blades:
1,Definition:
- Granulator blades are the cutting tools used in granulators, which
are machines designed to reduce the size of various solid
materials, such as plastics, pharmaceuticals, minerals, and
biomass.
2,Purpose:
- The primary purpose of granulator blades is to shear, slice, and
break down larger feed materials into smaller, more uniform
granules or particles.
- This size reduction is crucial for various downstream processing
steps, such as extrusion, injection molding, tableting, or further
refinement.
3,Blade Materials:
- Granulator blades are typically made from high-performance
materials, such as alloy steel, tungsten carbide, ceramic, or
specialized alloys, depending on the application and feed material
characteristics.
- The material selection is based on factors like hardness, wear
resistance, impact toughness, and corrosion/chemical resistance.
4,Blade Geometry:
- Granulator blades can have different blade edge geometries, such as
straight, serrated, or beveled, to optimize the cutting performance
for specific applications.
- The blade width, thickness, and bevel angle are also important
design parameters that can be customized to suit the granulator's
requirements.
5,Mounting and Configuration:
- Granulator blades are typically mounted on a rotor or drum within
the granulator, with a central mounting hole or multiple mounting
points to secure the blades in place.
- The number, arrangement, and orientation of the blades on the rotor
can be optimized to enhance the size reduction efficiency and
throughput.
6,Maintenance and Replacement:
- Granulator blades are subject to wear and tear during the size
reduction process and may require periodic sharpening, maintenance,
or replacement to maintain optimal performance.
- The frequency of blade maintenance or replacement depends on
factors like the feed material, operating conditions, and the
blade's material properties.
7,Regulatory Compliance:
- For applications involving food, pharmaceuticals, or other
regulated industries, the granulator blades must be approved for
use and comply with relevant safety and hygiene standards.
- The blade materials and design may need to meet specific regulatory
requirements, such as FDA or USDA approval for food-grade
applications.
Granulator Blade Specifications:
Product Name: | Granulator Screens Plastic Shredder Parts |
Material | Alloy Tool Steel D2 |
Length | 568mm |
Width | 100mm |
Thickness | 22mm |
Hardness | HRC 58-68 |
Precision | ±0.02-0.04mm |
Application | All kind of plastic |
When selecting the appropriate granulator blades, there are several
key factors to consider:
1,Feed Material Characteristics:
- Understand the properties of the feed material, such as hardness,
brittleness, toughness, etc., as these will influence the blade
material selection and geometric design.
- Different materials may require different blade designs to achieve
the desired particle size reduction and distribution.
2,Application Requirements:
- Based on the specific application, such as food, pharmaceuticals,
or plastic recycling, choose blade materials that comply with the
relevant safety and hygiene standards.
- Some applications may have special requirements for cutting
performance or wear resistance, which will also affect the blade
selection.
3,Particle Size Distribution and Control:
- Select the appropriate blade geometry and dimensions to achieve the
desired final product particle size distribution.
- The number, arrangement, and angle of the blades can all impact the
uniformity of the particle size reduction.
4,Machine Size and Mounting:
- Choose blade sizes and mounting hole diameters that match the
granulator's dimensions and assembly requirements.
- Ensure the blades can be securely installed on the granulator's
rotor or drum.
5,Wear Resistance and Longevity:
- Select blade materials with good wear resistance based on the
expected usage frequency and lifetime.
- Consider the periodic maintenance and replacement needs of the
blades to ensure continuous efficient operation of the granulator.
6,Energy Consumption and Cost-Effectiveness:
- Choose blade designs that can improve energy efficiency and reduce
the overall operating costs.
- Balance the blade's performance, durability, and cost to achieve
the best return on investment.
Picture:

Size:
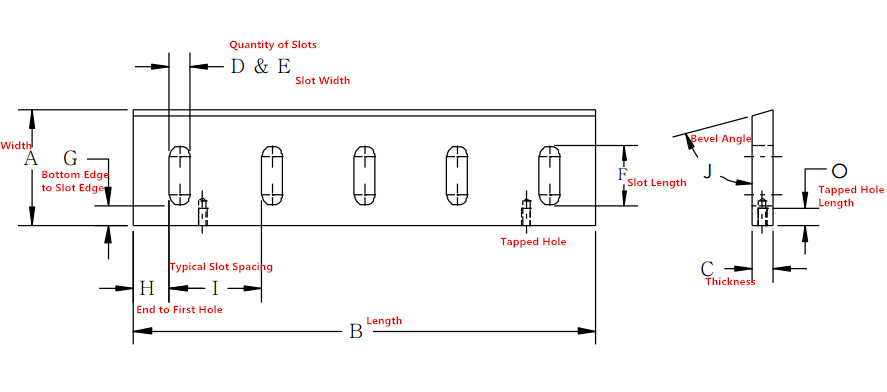
Applications:
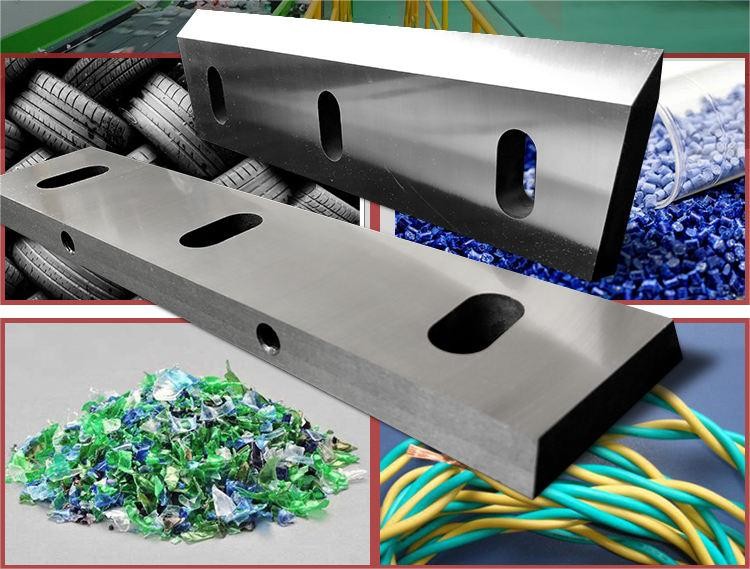
Packing & Delivery:
